Overview
In many industrial and public industries, explosion hazards are ever-present, e.g. the chemicals industry, refineries, on drilling platforms, gas stations, feed manufacturing and sewage treatment plants.
The risk of explosion is always present when gases, fumes, mist or dust are mixed with oxygen in the air in an explosive ratio close to sources of ignition that are able to release the so-called minimum ignition energy.
In the chemical and petrochemical industries in particular, when crude oil and natural gas are being transported, or in mining, milling (e.g. grain and granular solids), explosion can result in serious injury to persons and damage to equipment.
To ensure safety in these areas, legislators in most countries have implemented appropriate stipulations in the form of laws and regulations based on national and international standards.
Explosion-protected equipment is designed such that an explosion can be prevented when it is used properly.
The explosion-protected equipment can be designed in accordance with various types of protection.
The local conditions must be subdivided into specified zones by the user with the assistance of the responsible authorities in accordance with the frequency of occurrence of an explosion hazard. Device (equipment) categories are assigned to these zones. The zones are then subdivided into possible types of protection and therefore into possible equipment (product) types.
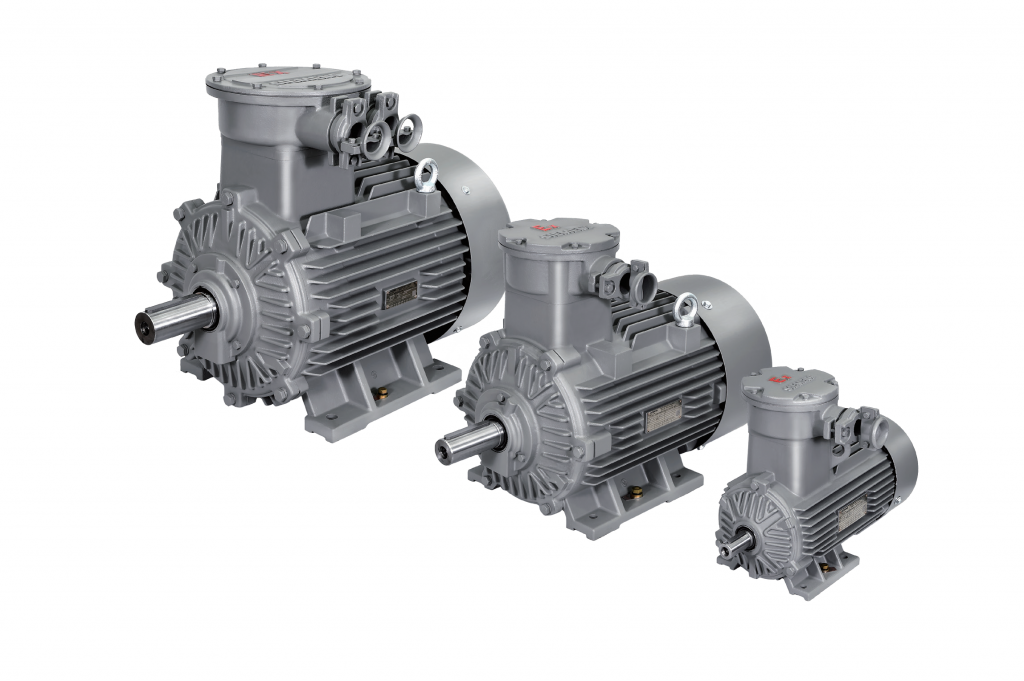
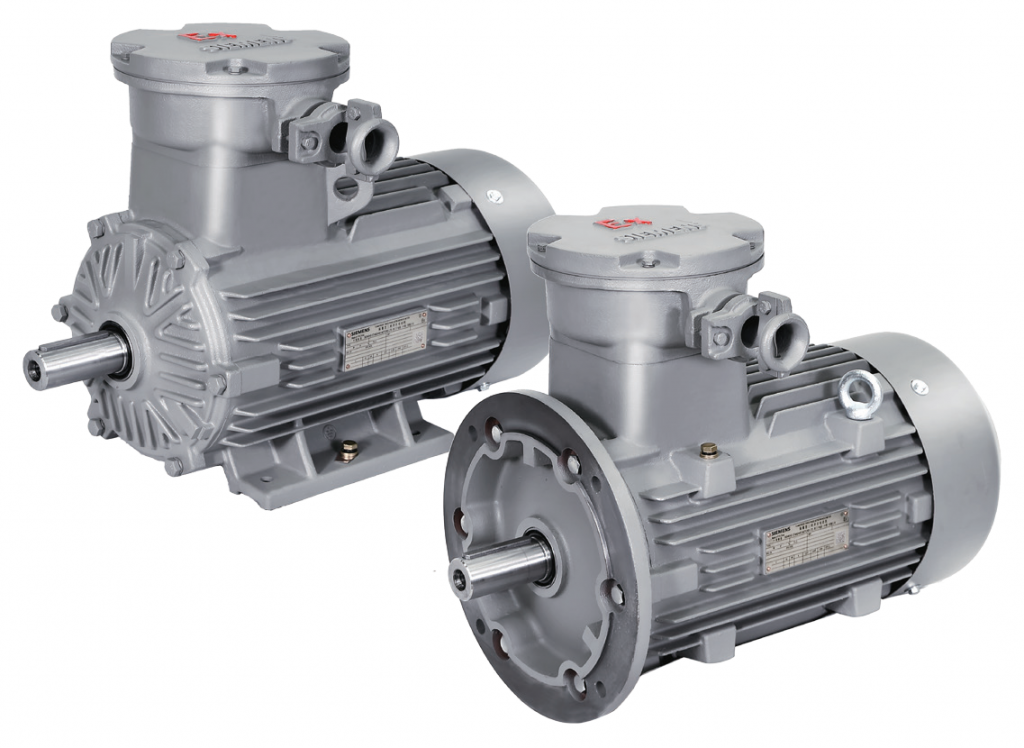
Classification of zones
Areas subject to explosion hazard are divided into zones. Zoning is based on the presence time of explosive substances and probability of explosion. Information and specifications for classification of the zones are laid down in the following standards:
Furthermore, a distinction is made between various explosion groups as well as temperature classes and these are included in the hazard assessment.
- GB 3836.14, IEC/EN 60079-10-1 for gas atmospheres
- GB 12476.3, IEC/EN 60079-10-2 for dust atmospheres
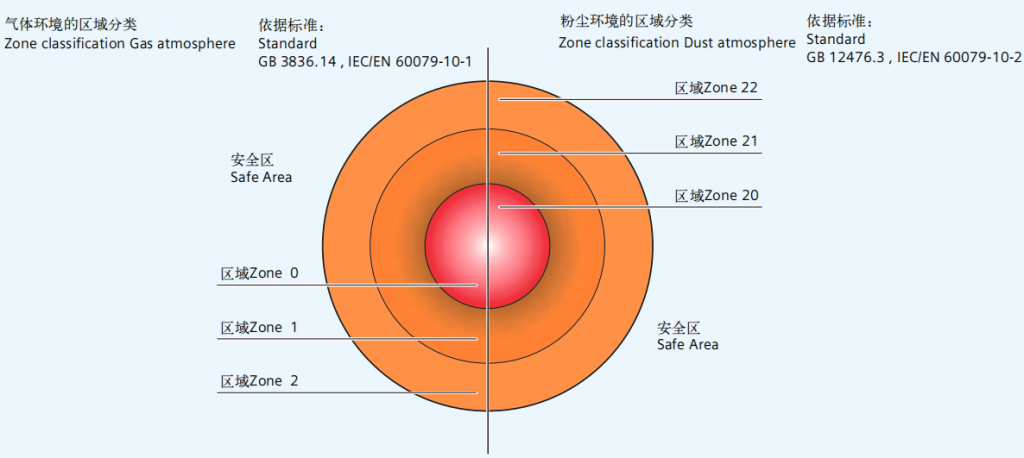
Depending on the particular zone and therefore the associated hazard, operating equipment must comply with defined minimum requirements regarding the type of protection. The different types of protection require corresponding measures to prevent ignition that should be implemented at the motor in order to prevent a surrounding explosive atmosphere from being ignited.
Gas 1)2) |
Dust 1)2) |
Zone definition acc. to GB3836.14 & IEC/EN 60079-10-1 for gas atmospheres GB 12476.3 & IEC/EN 60079-10-2 for dust atmospheres |
Assigned types of protection |
Category according to 2014/34/EU |
Equipment protection level acc. to GB3836.1 & IEC/EN 60079-0 |
0 | – | An area in which there is an explosive gas atmosphere constantly, over a long period or frequently. | Low-voltage motors not permitted |
1 | Ga |
1 | – | An area in which it is expected that an explosive gas atmosphere will occur occasionally during normal operation. | Ex e(GB) or Ex eb(IEC), Ex de, Ex d(GB) or Ex db(IEC) |
2 | Gb |
2 | – | An area in which it is expected that an explosive gas atmosphere will occur only rarely and then only briefly during normal operation. | Ex nA(GB) or Ex ec(IEC) | 3 | Gc |
– | 20 | An area in which there is an explosive gas atmosphere comprising a dust-air mixture constantly, over a long period or frequently. | Low-voltage motors not permitted |
1 | Da |
– | 21 | An area in which it is expected that an explosive gas atmosphere comprising a dust-air mixture will occur occasionally during normal operation. | Ex tb | 2 | Db |
– | 22 | An area in which it is expected that an explosive gas atmosphere in the form of a cloud of flammable dust in air will occur only rarely and then only briefly during normal operation. | Ex tc3) | 3 | Dc |
1) Motors of
– Zone 1 can also be used in Zone 2.
– Zone 21 can also be used in Zone 22.
2) Motors which are certified for gas or dust protection must not be used in hybrid mixtures! Hybrid mixtures: when explosive gas and dust atmospheres occur simultaneously.
3) Ex tc motors are not approved for operation in environments containing conductive dust.
Application
The explosion-proof motors are often used in the following industries to prevent explosion hazards that result in serious injury to persons and severe damage to property.
- Chemical and petrochemical industry
- Production of mineral oil and gas
- Gas works
- Gas supply companies
- Petrol stations
- Coking plants
- Mills (e.g. corn, solids)
- Sewage treatment plants
- Wood processing (e.g. sawdust, tree resin)
- Other industries subject to explosion hazards
Flameproof class of gases and vapors
Location | Code of standard GB3836.1 / GB3836.2 / IEC60079-0 / IEC60079-1 Flameproof class |
For Mines | d Ⅰ |
Explosive gas environment except mines | d Ⅱ A d Ⅱ B d Ⅱ C |
Temperature classes
Temperature class of electrical equipment | lMaximum surface temperature of electrical equipment | Ignition temperature of gases or vapors |
T1 | 450ºC | > 450ºC |
T2 | 300ºC | > 300ºC |
T3 | 200ºC | > 200ºC |
T4 | 135ºC | > 135ºC |
T5 | 100ºC | > 100ºC |
T6 | 85ºC | > 85ºC |
Classification of gases and vapors into explosion groups and temperature classes
explosion group | Temperature classes | |||||
T1(450) | T2(300) | T3(200) | T4(135) | T5(100) | T6(85) | |
Material designation | ||||||
IIA (MESG≥0.9mm) |
Acetone | i-amyl acetate | Benzine | Acetaldehyde | ||
Ethane | n-butane | Gasoline | ||||
Ethyl acetate | n-butyl alcohol | Special benzine | ||||
Ethyl chloride | Cyclohexanone | Diesel fuel | ||||
Ammonia | 1.2- dichloroethane | Heating oils | ||||
Benzene | Acetic acid anhydride | n-hexane | ||||
Acetic acid | ||||||
Carbon monoxide | ||||||
Methane | ||||||
Methanol | ||||||
Methyl chloride | ||||||
Naphthalene | ||||||
Pheno | ||||||
Propane | ||||||
Toluene | ||||||
IIB (0.5mm<MESG<0.9mm) |
Town gas (illuminating gas) |
Ethyl alcohol Ethylene Ethylene oxide |
Hydrogen sulfide | Ethyl ether | ||
IIC (MESG≤0.5mm) |
Hydrogen | Acetylene | Carbon disulfide |
•MESG, maximum experimental safe gap (for an explosive mixture). It’s maximum gap of a joint of 25 mm in width which prevents any transmission of an explosion during 10 tests made under the conditions specified in GB 3836.11 and IEC 60079-20-1.
•The smaller the MESG value, the higher the explosion-proof level of the equipment, and the more stringent requirements for the equipment. If the equipment can run under the IIC gas group, it also meets the requirements of IIA and IIB.
Contents
- The marking of flameproof motors
- Product overview
- Mechanical design
- Electrical design
- Converter fed application
- Order No. and Motor type
- Technical data table
- Options
- Dimension drawings
- Certificates